How Environmental Conditions Can Affect Heat Transfer Printing
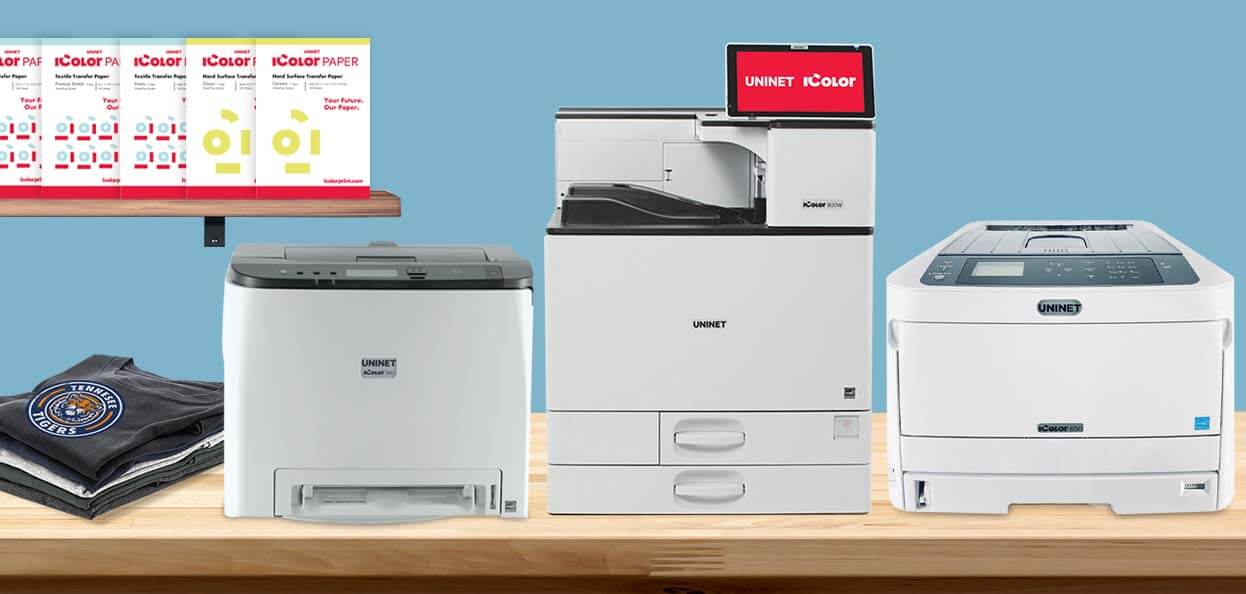
Toner Heat transfer printing is becoming a widely popular printing technology solution for many personalization and decorating businesses, hobbyists, and “DIYers”. Similar to other printing technologies such as sublimation, toner heat transfer printing creates the ability to put full-color images onto many types of hard and soft products, materials and substrates. In addition, toner heat transfer printing features low equipment maintenance, printing and transferring white, transferring to uncoated substrates and garments, printing on specialty papers and card stock, and more.
Customers who are new to a printing technology may experience a slight learning curve for their chosen technology, and toner heat transfer printing is no different. There can be challenges when creating those first few transfers, but don’t get discouraged. Many of the most common issues can be caused by the environment of the room where the printer is and where the transfers are made. Static electricity and humidity can impact the quality of prints and the functionality of the transfers in toner heat transfer printing.
Thankfully, there are some steps you can take to help mitigate the impact static and humidity can have on the toner heat transfer printing process. Understanding how they affect toner heat transfer printers and transfers can help you get the most out of your toner heat transfer equipment and supplies.
The shocking truth about static
Static electricity is one of the most common issues that arises in the toner heat transfer printing process. Dry environmental conditions are the leading cause of static electricity buildup, and are most often seen when using Two-Step transfer papers for garments and fabrics. The vast majority of these papers are made of a plastic cellophane sheet with a toner-receptive coating on one side. When the humidity of the surrounding environment is too low, static issues will occur. Some of the most common issues caused by static within toner heat transfer printing include:
There are a few simple ways you can help reduce the effects of static electricity on your toner heat transfer printing process. Some of those are:
The highs and lows of humidity
Another common environmental condition that can cause toner heat transfer printing issues is high or low humidity. For most printer models, the optimal operating humidity range is usually between 40-60% relative humidity. Some printer models may have humidity sensors built in to measure the current humidity level and automatically adjust the internal printer parameters to compensate for the current conditions. However, automatic printer adjustments might not be enough to compensate for wide variations in humidity levels.
If your printer comes with automatic humidity adjustments, the measured humidity levels should be available either from the printer menu, control panel, or displayed within the print configuration page.
There are some simple steps you can take to manage humidity levels in the room where you print and transfer. These steps can make a big impact on the success of your project and include:
Setting yourself up for success
As the seasons change and temperatures and humidity level fluctuate, it’s important to consider taking a few basic steps to control the environment where you’re doing your toner heat transfer printing and transfers. These steps will help avoid frustration and disappointing transfer results and make sure you’re delivering the best possible products to your customers. As always, our team of toner heat transfer experts are here to help as well. Give us a call at 800-869-7800 and ask to speak to one of our Advanced Support Team members for additional equipment support and troubleshooting help.