Equipment: Cutters
Cutters are arguably the most crucial piece of equipment you will ever work with because they are where the "rubber meets the road", or in our case, "where the tool meets the substrate". Nothing affects the outcome of the job more than selecting the proper cutter and making sure it cuts the way it's supposed to.
There are two basic materials used in the manufacture of rotating cutters, High-Speed Steel (HSS) and Carbide, or more technically correct, Tungsten Carbide (sometimes referred to "micrograin" carbide). Each material has advantages and disadvantages, so a brief explanation is necessary to aid you in proper tool selection.
HIGH-SPEED STEEL VS. TUNGSTEN CARBIDE
Cutters may be made with the entire shank and tip being manufactured from the same material, but the most common cutter in use today is actually a combination of the two. The carbide-tipped cutter consists of a piece of carbide braised onto a steel shank (Figure 3.12). The tool is slightly less expensive than the solid carbide version and slightly more expensive than the High-Speed Steel.
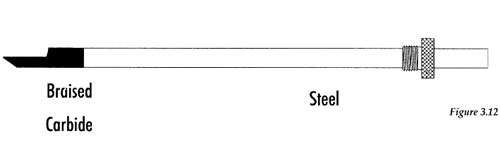
Carbide is an extremely hard but brittle material. It has excellent wear qualities and will remain sharp longer than HSS. It will produce a very high-quality cut, but due to its brittle nature, is susceptible to chipping and breakage and cannot tolerate vibration. Also, when sharpened it may not have the very fine cutting edge that can be achieved with an HSS cutter.
HSS may be ground to a perfect cutting edge. It does not have the wear qualities of Carbide but is much more forgiving and resistant to vibration and breakage during cutting. Although not as durable and wear-resistant as carbide, it does have greater tip resiliency for deep fine cuts in metal.
Here is a rule of thumb to use in deciding between Carbide and HSS: if you have the luxury of access to a cutter grinder and don't mind stopping after several plates to re-sharpen the tool, then HSS is a good choice. If you have a hundred plates to engrave and cannot afford the change over time and the interruption that comes from re-sharpening, then Carbide is the better tool for you.
TOOL CONSTRUCTION
Two types of tool construction exist, conical "half-round" and conical "quarter-round," and they can be easily recognized. Most engravers are familiar with the half-round version. This cutter is suitable for most applications, especially those requiring tool strength. Half-round cutters offer extra cutter strength due to the extra cutter material at the tip. Quarter-round cutters are good for applications in soft materials such as Plexiglas, acrylic, and aluminum. The reduced surface area can be beneficial in applications where cutter overheating is of concern. The smaller surface area helps to reduce cutter temperature and aids in chip clearance.
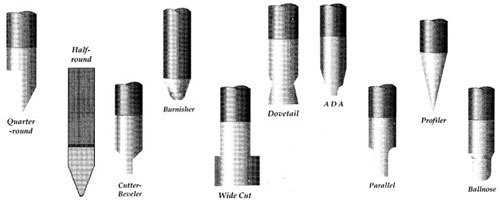
TOOL TYPES
There are several industry-wide designations for cutters. When ordering, use the following format and you will greatly increase the likelihood of getting the correct tool.
A typical part number for ordering cutters has significant digits and looks like this:
AC - 250 - .030
Always select the material type first, i.e. carbide tipped or solid carbide. The cutter prefix usually tells the supplier about the cutter material and about the size of the cutter shank required. In this case we may see a prefix of "AC" This tells us that the tool is a half-round carbide or carbide tipped. A designation of "ACQ" would indicate that the tool is a quarter round type. Each supplier may have his or her own part numbering scheme, so you need to become familiar with your supplier's catalog.
The size of .250* tells us that the cutter is has a 1/4" size shank.
* IF YOU ARE UNFAMILIAR WITH DECIMAL OR FRACTION MEASUREMENTS, PLEASE REFER TO THE CONVERSION CHART IN APPENDIX B. THIS CHART LISTS THE COMMON FRACTIONS AND THE EQUIVALENT DECIMAL AND MILLIMETER CONVERSIONS.
I cannot begin to tell you how many times I have seen the wrong size cutter ordered. No, not the tip size, but the tool shank size. It is important to understand decimals versus fractions and know the correct shank size of tool for your equipment. Three main types are standard in our industry. The size shank used is directly related to the engraving system spindle. Spindles are usually of two major families: those that will accept what I call a short shanked cutter of 4.5", and those that accept a long cutter of 6.5" or greater.

1/8" Shank - These tools are relatively small in diameter and in length. The common length they can be found in is 4.5". This tool was popular with some manual systems, the Dahlgren System 1, Wizzard II and XL models.

11/64" Shank - Many companies as a standard part of their equipment offering use 11/64" Shank. The tool length is usually 6.5" but can be 7.0" for those tools that must also be used in conjunction with a burnishing adapter.

1/4" Shank - The largest diameter tool used. Like the 11/64" tool, it is usually found in 6.5" or 7.0" lengths. Short 4.5" lengths can be found but are not considered as common.
The next part of selecting a cutter is to identify the material to be cut. Abbreviations are used to make the job easier and will often appear on the brass cutter knob for reference. The simple reason so many different cutters are offered is that each cutter has architecture unique to the material to be cut. Specific cutter angles are applied to help in the removal of chips during cutting, maximizing cutter strength, and cooling of the tool. These angles may not be apparent when viewing the cutter but none the less, they are important.
3-D: 3-D cutter with a long narrow tip for reverse engraving in acrylic, produces a three-dimensional effect.
ACR: Acrylic, Plexiglas, Lexan. Specify if for reverse engraving.
BAL: Brass and aluminum
BRN: Burnishing: For use on coated brass.
FLX: Flexible engraving stock: Rowmark, Innovative (IPI), Gravoply, Scott-Ply, Etc.
PHN: Phenolic
PRO: Profiler: narrow angle for strength and fine detail. Stronger than a parallel cutter, good for cut-outs.
PYR: Pyramid cutter for use on coated pens. Not for chrome, steel, gold etc.
RUB: Rubber stamp matrix
SSS: Stainless Steel
Last is the designation of the cutter tip size. Cutters are generally sharpened in .005" increments starting at .005" up to the size of the cutter shank. Therefore, a cutter with an 11/64" shank can be offered with a tip up to .171". The tip size selected is determined by the height of the engraved character. Cutter tip width will also play a role in determining the boldness of any logo or graphic used. See the tip selection chart in Appendix B.
HOW TO SELECT THE RIGHT CUTTER
Selecting the right cutter is not an exact science. Factors such as your own preferences, the preferences of your client, and the needs of the job come into play. However, some generalizations can be made. I've tried to highlight some basic requirements based on the engraving method or substrate you may be using:
Plastic Engraving Stock - Have a good selection of FLX cutters in sizes such as .005, .010, .015, .020, .030, .045, .060, .125, .171, and .250 on hand and keep back-ups for any sizes that you routinely use. It's good to have a spare should you break one or need to send worn cutters in for re-sharpening
ADA Signage - You'll most likely need a Braille cutter as well as a profile cutter to cut out the required raised letters. Profile cutters are usually sharpened to 15-degree angles and have a .015 tip. They are prone to breaking and it may be good to have extras around for other applications as well. Braille cutters may be unique to your engraving software program. Consult the software or equipment supplier for recommendations on the proper Braille cutter for your program.
Cut-Out Letters, Shapes, etc. - My first choice is a profile cutter. Due to the cutting angle, 15 degree, you will see a bit of the core material when cutting through plastic. I find this attractive in most applications but sometimes a straight 90-degree cut is important. In this case, choose parallel cutters with the correct architecture for the type of cut-out work you do. If the materials you cut out are different thicknesses, you'll need a different cutter for each. These cutters are specially sharpened to give you the maximum strength and to avoid breakage. You can also use the standard FLX cutters for cut-outs, which will result in a 30-degree angle. Ask the supplier for details.
Stainless Steel or Deep Engraving on Metals - Order these as needed. If you get a particular application such as a control panel and need different sizes, order two of each. Cutting harder materials will dull the cutter sooner and you'll want a back up as protection against cutter breakage.
Brass, Aluminum, and Glass - For trophy brass and aluminum you will need burnishing cutters. For glass you must use rotating diamond cutters. These come in several shank lengths and tip sizes. Choose the size that fits your spindle or adapter* and produces the correct width of cut for the letter size required. Drag diamonds (for fine lines on metal) are the least expensive. Rotating diamonds (for glass and burnishing on metal) will be two to three times more expensive. For very large stroke widths on metal, you may consider carbide burnishers instead of rotating diamonds to reduce the cost.
GRINDING YOUR OWN CUTTERS
If you are willing to learn the techniques and can make a significant investment in the equipment, you can grind your own cutters. This can give your operation several advantages such as the ability to reduce your overall cutter inventory, keeping cutter-dependent jobs running, and the ability to experiment with tool geometry to get the best results. Larger shops or those with high cutter usage may find a grinder beneficial. If you are new to engraving or operate a small business, a cutter grinder may not be a good investment. Keep in mind that cutter grinding takes a bit of skill and patience. This may not be something that you want to tackle since there are plenty of shops that will perform this service for you (Johnson Plastics Plus provides a sharpening service for your cutters). Also, grinders are unique to the industry and therefore can be expensive. A cutter sharpener may be as little as $1,500 while a true cutter grinder with all the bells and whistles can cost as much as $5,000. An inexpensive grinder designed primarily for use in re-sharpening is what most engraving shops require. A true grinder with various grade grinding wheels is used by those engravers that will make tools from cutter blanks. A grinder is not something that you need to invest in initially.
TOOL LIFE
The cutting conditions that determine the rate of metal removal are the cutting speed, the feed rate, and the depth of cut. These conditions and the nature of the material to be cut determine the power required to "take" the cut. Cutting conditions must be adjusted to stay within the power available on the particular machine you're using.
Cutting conditions must also be considered in relation to tool life. Tool life can be defined as the length of time that a cutting tool will cut before it becomes dull or must be replaced. Eventually, the amount of wear on the flank of the tool will make it unusable. Exactly how long cannot generally be predicted since equipment type, care, tool material and the kind of cutting are interrelated and different for every shop and every job.
The good news, of course, is that an unbroken tool with normal wear may be sharpened several times - therefore reducing the expense of replacement.
ROUTER BITS
These tools are generally designed for use in high-speed routers but can often be used in collet type engraving spindles. Although routing is only discussed in limited detail later, it's important to realize that you have many more tool options than those offered by traditional engraving bits. Along with some minor hardware and software considerations, you have unlimited ability. Here are the more common types of tools you may encounter.
TOOL GEOMETRY
Straight flute - These cutters do not allow for the lifting of material or chips out of the cut. When a smooth finish in wood and plastic materials are required, this is a good choice.
Double flute - With two cutting edges, these bits provide a better finish, especially in harder materials.
Multi-fluted - Many tools may have more than one or two flutes. Oftentimes, end mills will have three, four or more flutes. These tools can be extremely effective when a very smooth edge is desired and will generally stay sharp a long time. X-Y movement through the workpiece will be much slower, however.
FLUTE GEOMETRY
Single flute - These cutters have only one cutting edge; therefore, they can be used for faster feed rates.
Double flute - Having two cutting edges, these bits provide a better finish, especially in harder materials.
Upcut spiral - Upward chip removal occurs when using this bit. Used for grooving, slotting, hog outs and whenever a good finish is required on the bottom side of the material being machined. This bit can be tricky because it will have a tendency to pull up on the material when plunging.
Downcut spiral - Downward chip removal occurs when using this bit and it eliminates more vibration by forcing the material down. Use this bit when requiring a good finish on the topside of the material.
Up/Down Spiral - This bit should be used for double laminated materials when requiring the best finish on both the top and bottom sides of the material.
DESCRIPTIONS OF CUTTERS
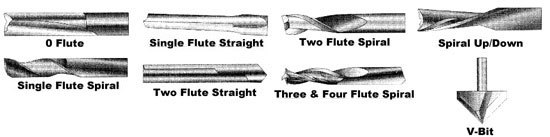
0 flute - Half-moon shaped, single fluted, used in soft to medium woods and flexible non-abrasive plastics.
Single flute straight - For faster feed rates and freedom of cutting action, for general use in almost any material. A good bit to try when all else fails.
Single flute spiral - (TC or HSS) Used for larger-chip and more-effective heat removal in jobs requiring higher cutting speeds. Good for aluminum, natural woods and non-abrasive plastics.
Two flute straight - Has a much longer life and better tool balance. Will produce a smooth finish in laminates, Plexiglas, natural wood and fiberglass.
Two flute spiral - (TC or HSS) Provides a smoother finish when grooving, slotting or blind routing. A good general purpose tool to cut almost any material. Especially good for plastic, wood and aluminum.
Three & Four flute spiral - Good for cutting very abrasive materials. These will usually be an up-cut design. Spiral up/down (Compression) - For fast feed rates and best finish on both sides of the material. Used for cutting double-sided laminates, hard woods and wood composites.
V-Bit - Good for 3-D relief carving as well as grooving. Usual angles found are 60, 90 & 120 degree. This is a good "general purpose" tool.
Some cutters, such as two-flute, spiral-up cutters, can be used for both acrylic and aluminum cutting, but never use the same tool on acrylic after cutting aluminum. Aluminum has a tendency to "load up" or deposit on the tool. This will prevent good cutting of acrylic. In this case, stock two cutters of the same geometry, one for each material.
The Engravers' Bible © 1999 by Rich Zydonik/National Business Media, Inc. Printed and Bound in the United States of America. All rights reserved. No part of this self-study manual may be reproduced in any form without permission in writing from the author/publisher. Additional legal, financial and professional management advice and/or assistance are encouraged.